
Revolutionary manufacturing process: the rise of hot drilling and hot drawing
In this ever-changing era, the manufacturing industry is constantly seeking new breakthroughs. In recent years, two remarkable technologies-hot drilling and hot drawing, are quietly changing the traditional processing methods. Compared with the methods that used to rely on human or simple mechanical operation, now we can see a completely new scene is taking shape.
In the past, many complex parts processing faced many difficulties, such as time-consuming, lack of precision and other issues. With the progress of science and technology, these problems have been effectively solved. Taking aero-engine blades as an example, in the past, it took a lot of time and energy to make such precision parts, and the qualified rate of finished products was not high. Now with the support of hot drills and hot pulls, everything is different. By precisely controlling the temperature and pressure parameters, not only greatly improves the production efficiency, but also ensures that every detail meets the high standard requirements.
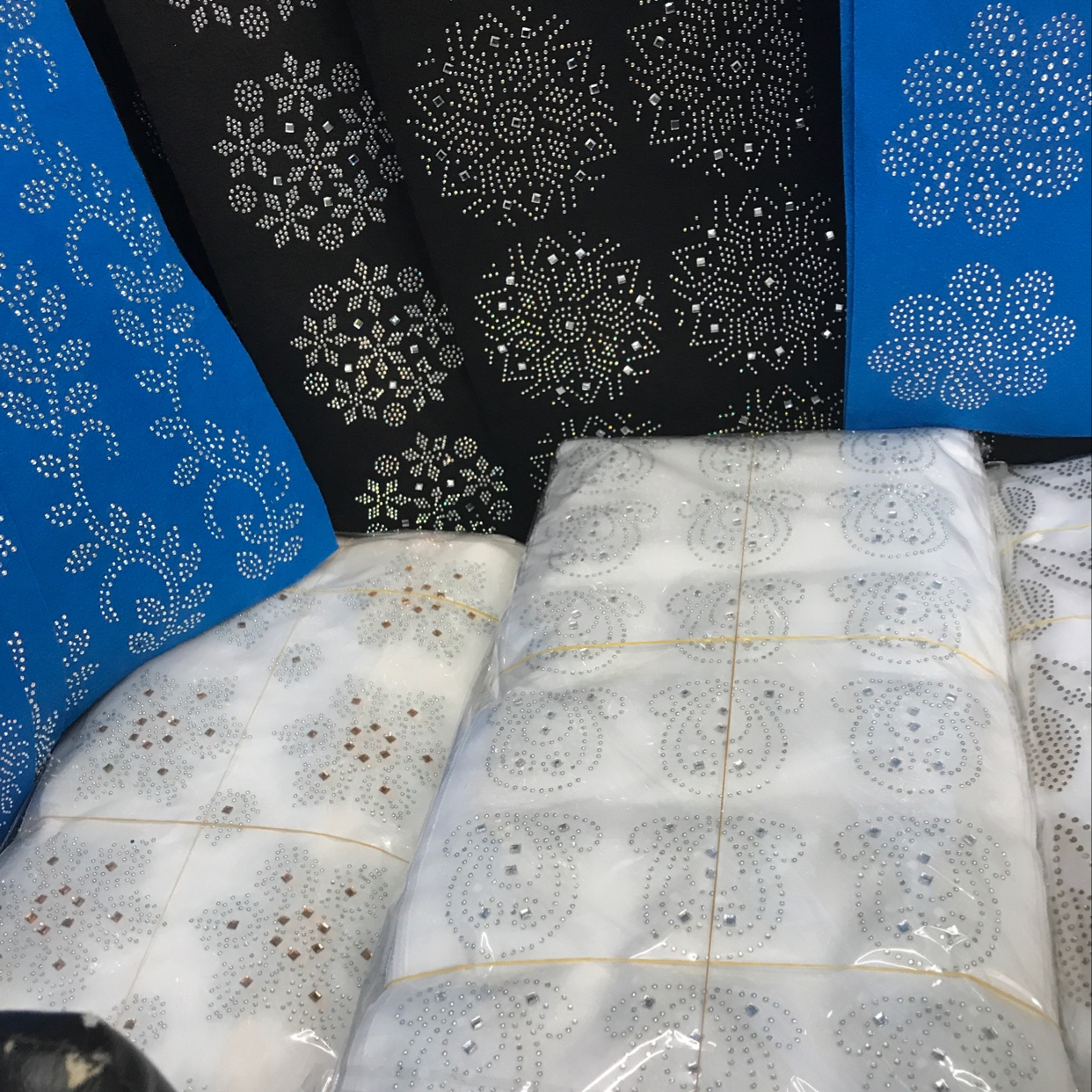
The reason why these new technologies stand out is that they fundamentally solve the bottleneck problems in the old process. Whether it is from the perspective of material utilization, or looking at the quality and performance of the final product, we have seen significant progress. It can be said that this is a major leap in the manufacturing industry, and it also points out the direction for future development.
The secret weapon of high efficiency and precision: the working principle of hot drill
As an innovative drilling tool, the core of the hot drill is to use local high temperature to melt the surface of the processed object and then carry out the process of rapid cooling molding. The key elements involved in this process include: precise heat distribution control, instantaneous completion of condensation and solidification, and a stable advance rate. All of this is to ensure that the holes are smooth and tidy, free of burrs and other defects.
according to the latest research report, compared with the traditional EDM or other forms of manual equipment, the use of hot drills can obtain better dimensional accuracy (within ± 0.02mm) and faster speed (a single small hole with a diameter of φ 2mm can be completed in one second). More importantly, it is also excellent for difficult-to-cut alloy steel, titanium matrix composites and even ceramic products, greatly broadening the scope of application.
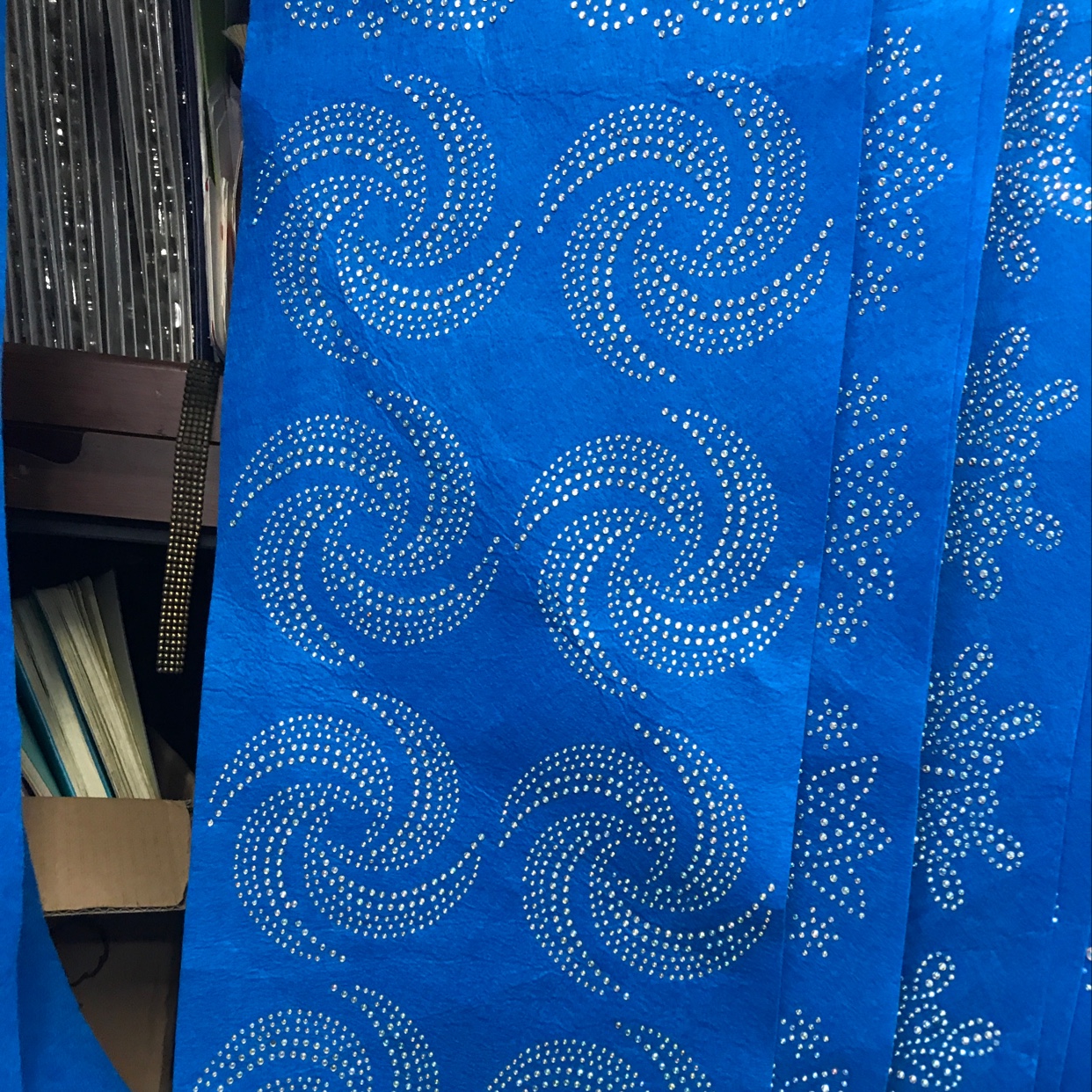
In addition, it is worth noting that due to the special wear-resistant coating design, the tool life is extended many times, thereby reducing the number of replacements and maintenance costs. This is undoubtedly a great boon for industrial enterprises pursuing efficient production. Therefore, whether in the scientific research laboratory or large-scale production line environment, people are increasingly inclined to choose this kind of technical scheme which is economical and can guarantee high-quality output.
The perfect partner for seamless connection: the technical highlight of hot drawing
If hot drills are good at handling small and delicate tasks, hot drawing is known for its powerful shaping ability. Different from the regular sense of cold drawing or forging forming means, the latter is usually only for the soft state of the metal to implement a greater degree of deformation, and the former can be close to room temperature conditions easily do this, and will not cause any micro cracks or coarse grain side effects.
Specifically, when an originally flat and hard plate enters the main working area after the preheating stage, the machine will apply uniform pressure to expand it in the longitudinal direction according to a predetermined program. At this time, the relationship between the heating curve and the force distribution ratio must be strictly controlled, otherwise it is easy to cause irreversible damage. However, once you master the correct operation skills, you can get an extremely smooth and beautiful curved surface effect.
In fact, high-end equipment manufacturing industries such as aircraft skins and automobile shell frames have already begun to widely use such methods for mass production tasks. Thanks to its unique "mild" nature, it not only reduces unnecessary energy consumption, but also greatly reduces the workload of the subsequent finishing process. In short, this is a very ideal choice, especially in the face of those who have high requirements for appearance and texture.
Win-win situation: resource saving and environmental protection
The use of hot drilling and hot drawing technology not only brings economic benefits to enterprises, but also promotes the development of the whole society in a more environmentally friendly direction. The first is reflected in the utilization of raw materials, because these two processes allow us to better plan the best use of each piece of material and almost completely eliminate the presence of scrap. The second is the optimization of energy consumption indicators. According to statistics, the electricity required by products of the same specification per unit time is about 30% lower than the original.
In addition, what is more important is that they are all products in the category of clean energy, and there is no risk of harmful substance emission. In the context of global advocacy of low-carbon life, this is undoubtedly a concrete manifestation of many manufacturers actively responding to the call. Of course, this also means that more consumers are willing to buy goods produced by such green factories, indirectly promoting a virtuous circle in the market.
All in all, whether it is for self-interest or social responsibility, the introduction of such an advanced and reliable system architecture should be given priority. After all, only everyone can work together to create a better tomorrow!
Quality leap: finished product consistency and stability
With the increasingly stringent market demand, customers have higher and higher requirements for product quality. In this regard, hot drilling and hot drawing show an unparalleled advantage. Through the fine management of a series of key links, each factory inspection project can meet the standard or even exceed the expected value. In particular, great progress has been made in the two important dimensions of geometric error tolerance and surface roughness.
According to data, since the second half of last year, after a well-known electronic component supplier implemented a new processing specification in its interior, the rework return rate has plummeted by nearly five percentage points. At the same time, the number of orders has shown a steady upward trend. Obviously, high quality products have become one of the indispensable factors to win market share. Not only that, brand reputation has also been greatly improved.
Let's look at another example. A leading domestic medical device manufacturer once faced a similar dilemma: although it has a top R & D team and technology