
The origin of technology: the development of hot drilling and hot drawing
Since the birth of hot drilling and hot drawing technology, it has experienced an evolution from an innovative concept to a wide range of applications in various industrial fields. Initially, these two technologies were used to solve specific industrial problems. With the advancement of technology and the growth of market demand, they gradually developed into efficient heating solutions. Through continuous technological innovation and optimization, hot drilling and hot drawing have become the leader in the field of industrial heating. They not only improve production efficiency, but also significantly reduce energy consumption, has become the first choice of many enterprises.
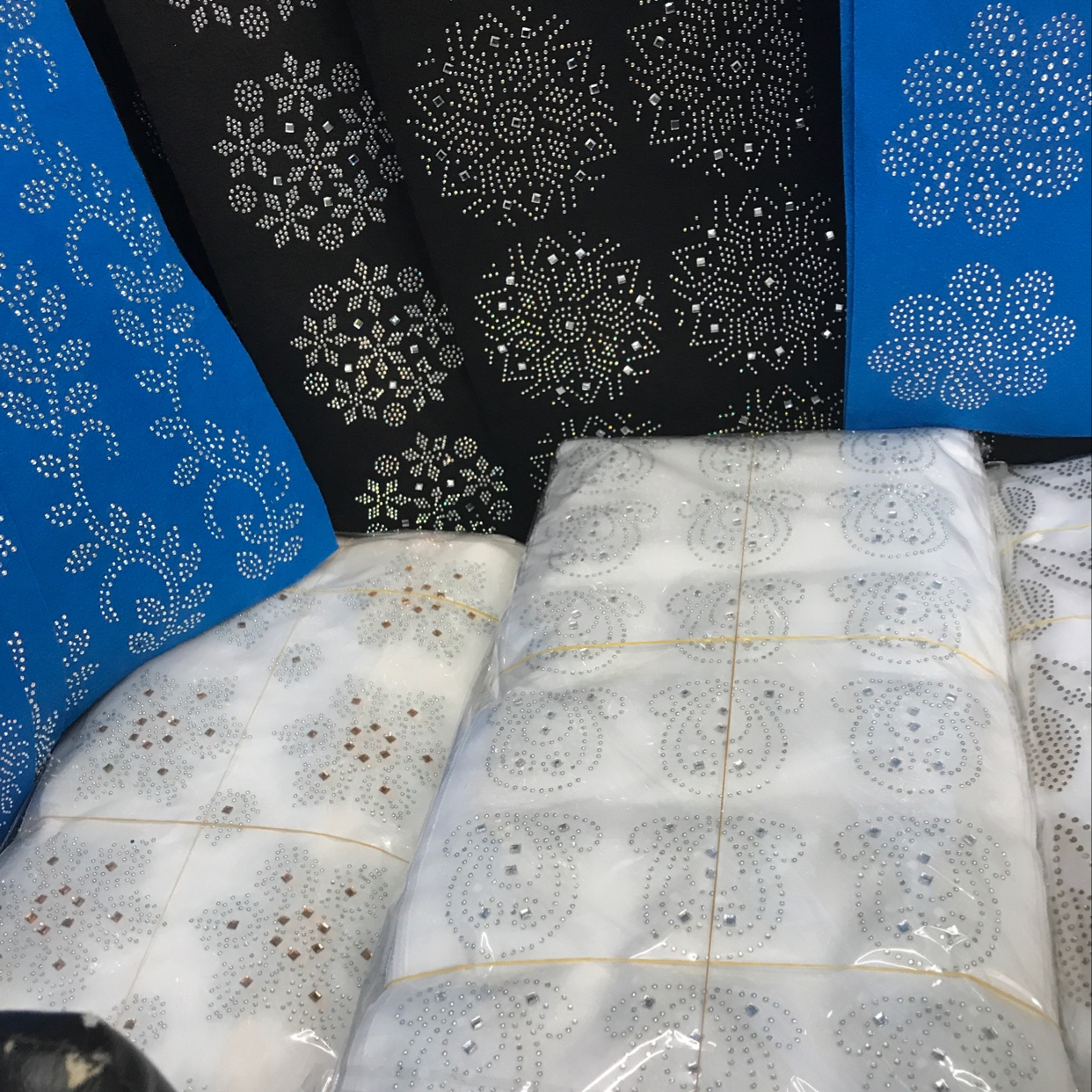
Working principle: efficient heating mechanism
The core of hot drilling and hot drawing technology lies in its efficient heating mechanism. The hot drill generates a large amount of heat in a short time through high-speed rotation and local heating, and quickly reaches the required temperature. The thermal pull is the use of resistance heating principle, through the precise current control of the material, to achieve uniform and controllable heating effect. Both technologies can achieve rapid heating and cooling, greatly shortening the process time and improving production efficiency. Through diagrams and diagrams, we can more intuitively understand how these technologies work.
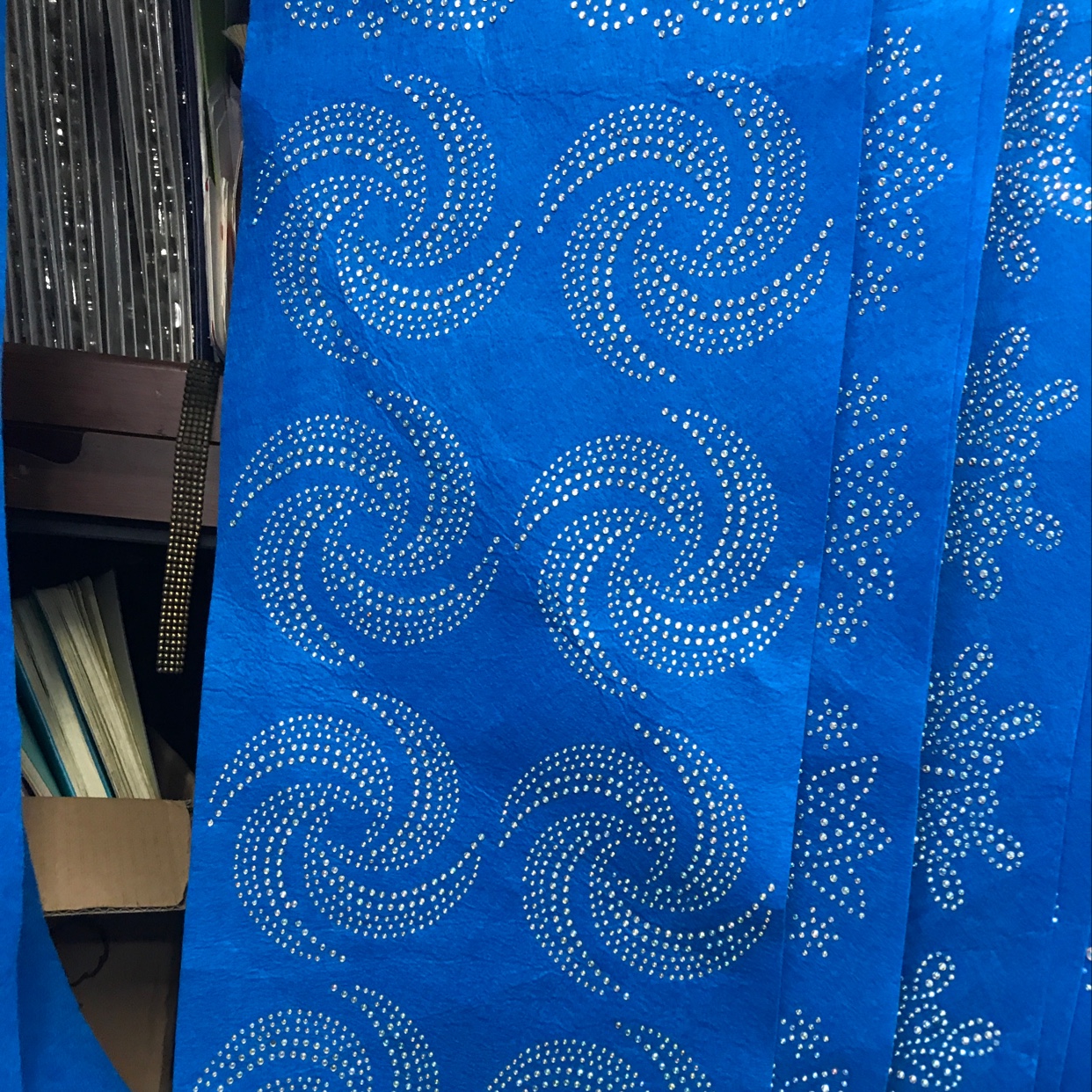
Performance Advantage: Increased Productivity and Reduced Energy Consumption
Hot drilling and hot drawing technologies are outstanding in improving production efficiency and reducing energy consumption. Compared with traditional heating methods, they can significantly shorten the heating time and cooling time, thus speeding up the production rhythm. In addition, due to their efficient energy conversion rate, these technologies also have obvious advantages in energy consumption. A number of studies have shown that enterprises using hot drilling and hot drawing technology can save more than 20% of energy consumption on average. This data not only reflects the superiority of the technology, but also brings real cost savings to the enterprise.
Application Scenario: Metal Processing and Plastic Molding
Hot drilling and hot drawing technology are widely used in different industrial fields. In the metal processing industry, hot drilling technology is widely used for precision drilling and cutting, which can achieve high-precision and high-efficiency processing. In the field of plastic molding, hot drawing technology is used for mold preheating and plastic molding to ensure product quality and consistency. Through specific application cases, we can see how these technologies solve the pain points of the industry and improve production efficiency and product quality.
Customer Success: Real Application Witness
Many companies have achieved remarkable results after introducing hot drilling and hot drawing technology. For example, a metal processing enterprise through the use of hot drilling technology, the drilling speed increased by 30%, while reducing the rejection rate. Another plastic products company uses hot pull technology to achieve higher mold preheating efficiency and shorten the production cycle by 25%. These successful cases not only demonstrate the effectiveness of the technology, but also provide valuable lessons for other enterprises.
Maintenance: Ensure long-term stable operation of equipment
In order to ensure the long-term stable operation of hot drilling and hot drawing equipment, we need regular maintenance and maintenance. It is recommended to regularly check the key components of the equipment, such as motors, heating elements and control systems, to ensure that they are in good working condition. In addition, clean up the dust and debris on the equipment in time to prevent the failure caused by dust accumulation. For wearing parts, it is recommended to replace them according to the schedule recommend by the manufacturer to extend the service life of the equipment.
Technology Innovation: Future Development Direction
The future development prospects of hot drilling and hot drawing technology are very broad. At present, researchers are actively exploring new materials and processes to further improve the performance of these technologies. For example, the development of higher temperature resistant heating elements to improve the service life of the equipment; optimization of control algorithms to achieve more accurate temperature control. These technological breakthroughs will further enhance the competitiveness of hot drilling and hot drawing in the field of industrial heating, and bring more opportunities for enterprises.
Selection Guide: How to Choose the Right Heating Scheme
Choosing a suitable heating scheme requires comprehensive consideration of multiple factors. First, evaluate your own production needs and identify the type of material and temperature range to be heated. Second, consider cost-effectiveness and compare the return on investment of different technologies. Finally, choose a supplier with experience and technical strength to ensure the quality of the equipment and service support. With this step, you can be more confident in choosing the heating scheme that suits you best.
Environmental protection concept: a model of green manufacturing
The contribution of hot drilling and hot drawing technology to environmental protection cannot be ignored. They not only significantly reduce energy consumption, but also reduce waste generation and improve resource utilization. By adopting these technologies, many enterprises have achieved the goal of green manufacturing and made positive contributions to environmental protection. As a responsible company, we are also committed to promoting these environmentally friendly technologies and building a sustainable future together.
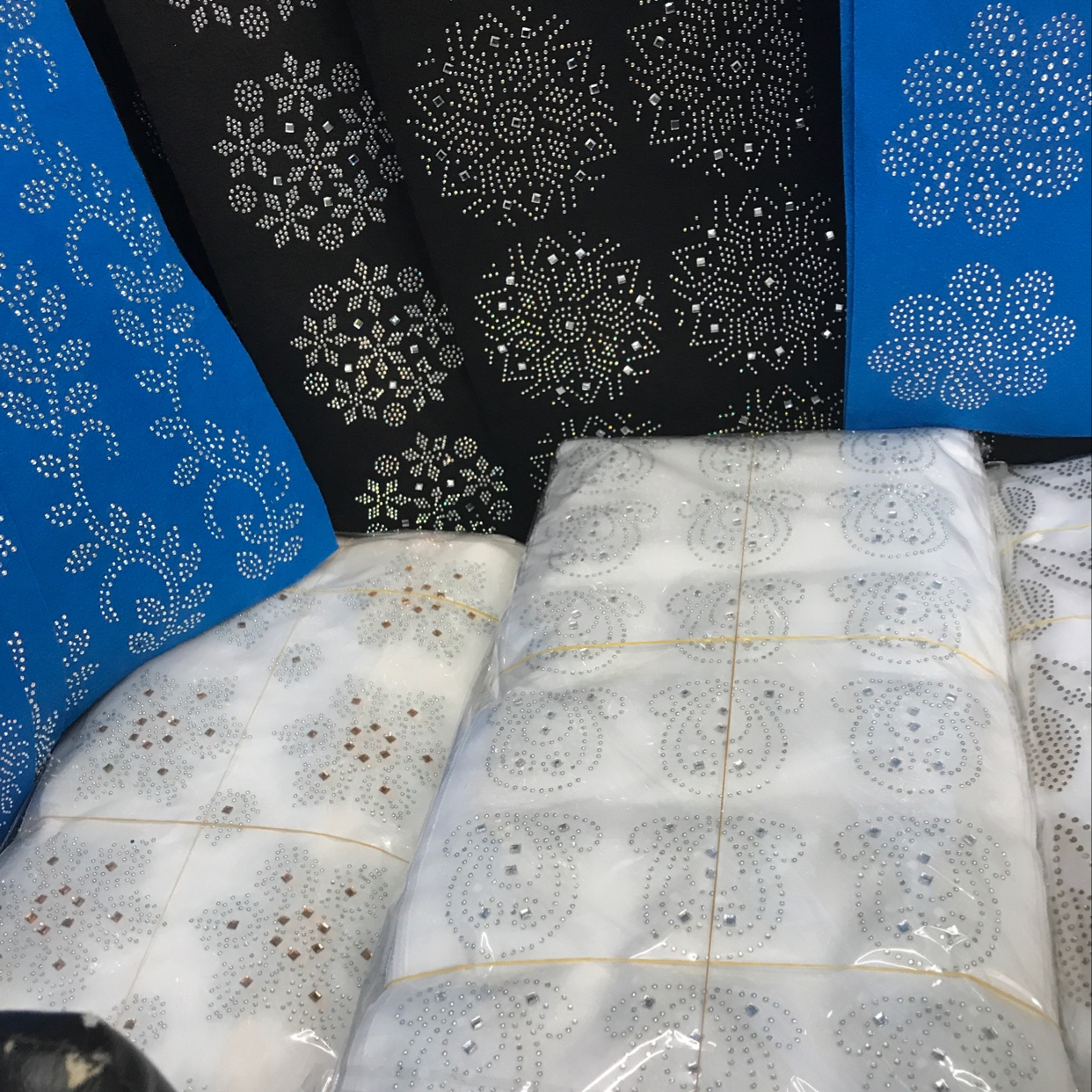