
Application background of hot drilling and hot drawing
In modern industrial processing, problems such as low production efficiency, high cost, and unstable quality have been plaguing enterprises. To overcome these challenges, hot drilling and hot drawing have become indispensable and efficient tools. Hot drilling is a fast and efficient hole processing tool, while hot drawing is a precise material forming process. These two tools can not only significantly improve production efficiency, but also ensure the quality of processing, suitable for a variety of materials and application scenarios.
The development history of hot drilling and hot drawing can be traced back to the end of the last century. With the advancement of material science and mechanical technology, they have gradually been widely used in various industries. Today, these tools have become the standard configuration of many enterprises, helping enterprises to improve their competitiveness.
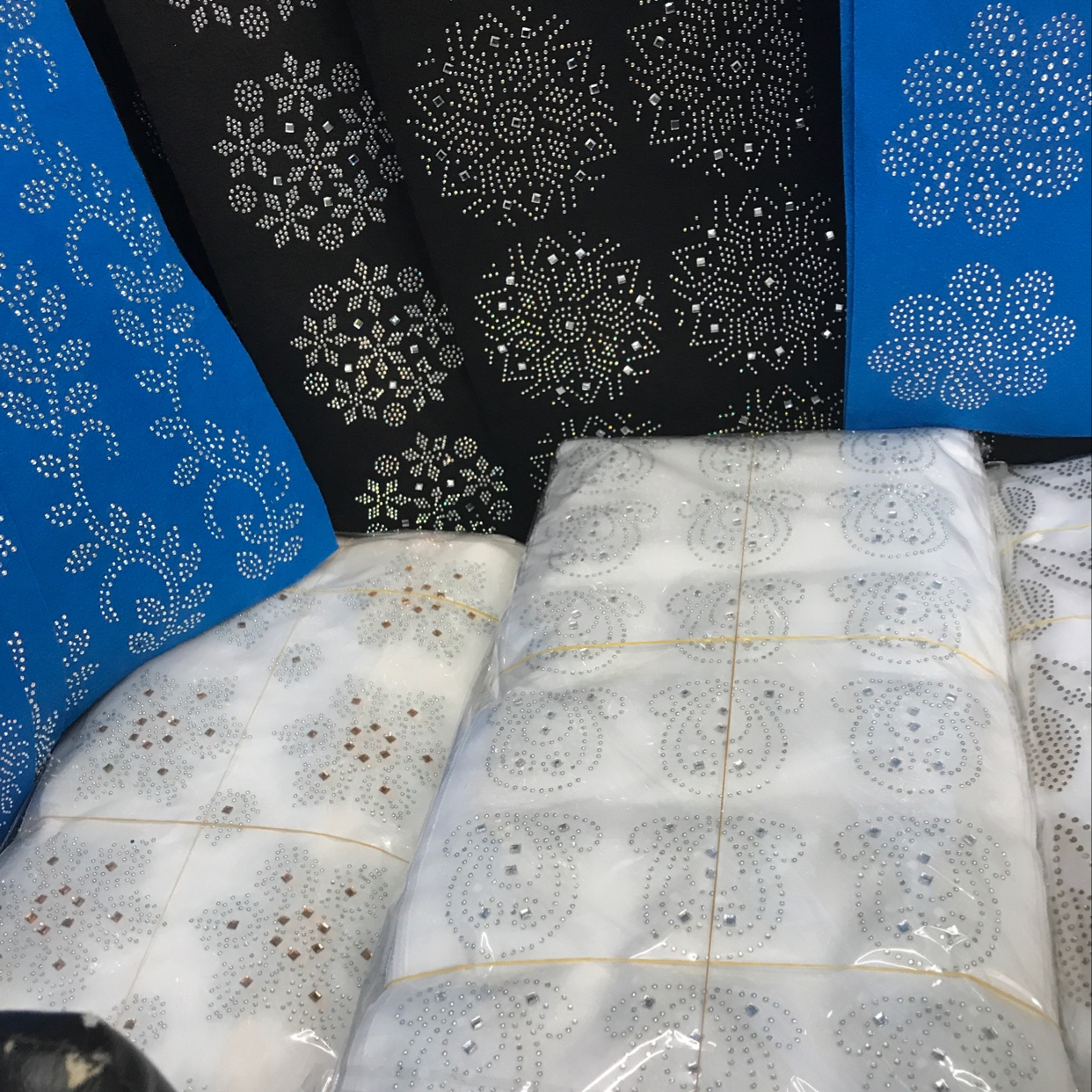
Hot Drill: Fast and Efficient Hole Machining Tool
The working principle of the hot drill is based on high-speed rotation and high-temperature heating. When the hot drill bit comes into contact with the surface of the workpiece, a local high temperature will be generated, causing the material to melt instantly. Then, the drill quickly passes through the molten material, forming a smooth hole. This process is not only fast, but also high precision, suitable for metal, plastic and other materials.
In the automobile manufacturing industry, hot drills are widely used in the processing of body parts. For example, in the manufacturing process of automobile door frames and bumpers, hot drills can quickly and accurately punch the required holes, which improves production efficiency. In the field of aerospace, hot drilling also plays an important role, especially in the processing of high-strength alloy materials, the high efficiency and reliability of hot drilling has been fully reflected.
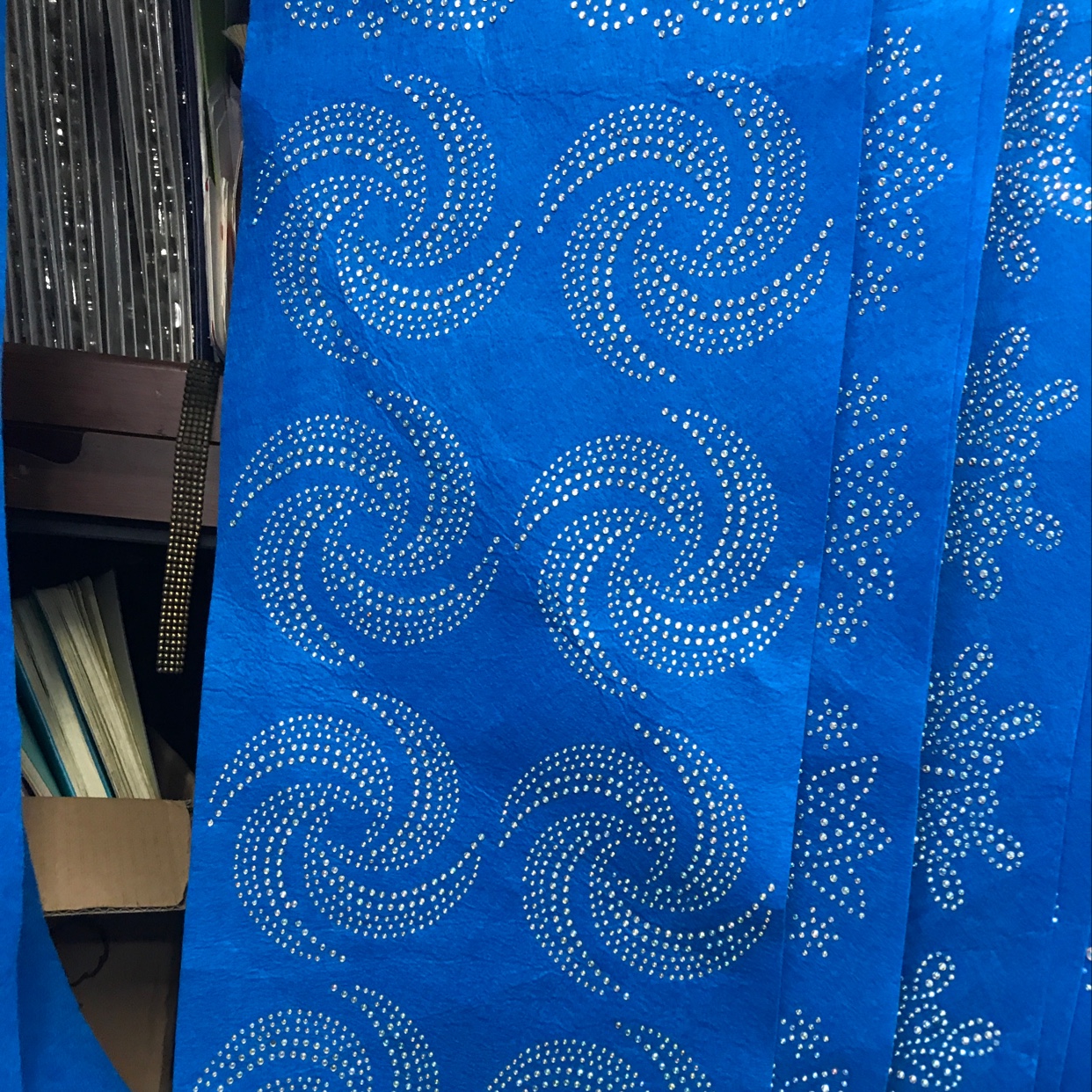
Hot drawing: precision material forming process
Hot drawing is a process that uses high temperature and pressure to shape materials. In the hot drawing process, the material is heated to a plastic state and then stretched or compressed by a mold to achieve the desired shape and size. Hot drawing technology has the advantages of high precision and high consistency, especially suitable for the processing of fine parts.
In the manufacture of electronic components, hot drawing is widely used to produce small parts such as connectors and pins. These parts require extremely high precision and consistency, and hot drawing technology can meet these demanding requirements. In the field of medical devices, heat pull also plays an important role, such as the production of syringes, catheters and other medical equipment to ensure their safety and reliability.
Common advantages of hot drilling and hot drawing
Hot drilling and hot drawing have common advantages in improving production efficiency, reducing costs, and ensuring processing quality. First of all, the processing speed of these two tools is very fast, which can greatly shorten the production cycle. Secondly, their high precision ensures the consistency and quality of each part. In addition, the operation of hot drilling and hot drawing is simple and easy to master, reducing training time and labor costs.
Many users have given high praise in actual use. A car manufacturer said: "Since the introduction of hot drilling and hot drawing technology, our production efficiency has increased by 30%, and the quality of our products has also improved significantly." Another medical device company also said: "Hot pull technology makes our products more sophisticated and significantly improves customer satisfaction."
Choosing the right hot drill and hot pull tools
Choosing the right hot drill and hot pull tools requires a comprehensive consideration of processing needs and budget. For metal processing, you can choose high-speed steel hot drill; and for plastic processing, you recommend use carbide hot drill. The choice of hot pull tool needs to select the appropriate mold and heating method according to the specific material and molding requirements.
There are many well-known brands and models of hot drills and hot drawing tools on the market, such as XYZ's high-performance hot drill series and ABC's precision hot drawing system. Each tool has its own unique characteristics and scope of application. It is recommended to know the product parameters and technical support of each brand in detail before purchasing.
Practical application cases of hot drilling and hot drawing
The application cases of hot drilling and hot drawing in many industries show their excellent performance. For example, a household appliance enterprise in the production of refrigerator panels, the use of hot drilling technology for the processing of screw holes. The results show that the processing time is shortened from 1 minute to 10 seconds, and the hole position accuracy reaches 0.01mm. This not only improves production efficiency, but also reduces the scrap rate.
Another medical device company used hot drawing technology to form the needle tube when producing disposable syringes. Through precise control of temperature and pressure, the company successfully achieved high precision and high consistency of the needle tube, and the product qualification rate reached 99.9 percent. These practical cases fully prove the important role of hot drilling and hot drawing in improving production efficiency and quality.
Operation and Maintenance Skills
Correct operation and maintenance are the key to ensuring the long-term stable operation of hot drills and hot drawing tools. Before use, should carefully read the instructions, familiar with the operation steps. In daily use, the following points should be noted:
1. Regularly check the wear of tools and replace damaged parts in time.
2. After use, the residue on the surface of the tool should be cleaned in time to prevent blockage and corrosion.
3. When storing tools, they should be placed in a dry and ventilated place to avoid moisture and rust.
4. in case of failure, should contact professional and technical personnel for maintenance, do not disassemble.