
In-depth understanding of hot drilling and hot drawing technology, these two methods based on high-temperature processing are changing the face of jewelry manufacturing and other precision processing fields. This article will analyze their working principles, application scenarios and the innovative breakthroughs they bring in detail to reveal the charm of this cutting-edge technology.
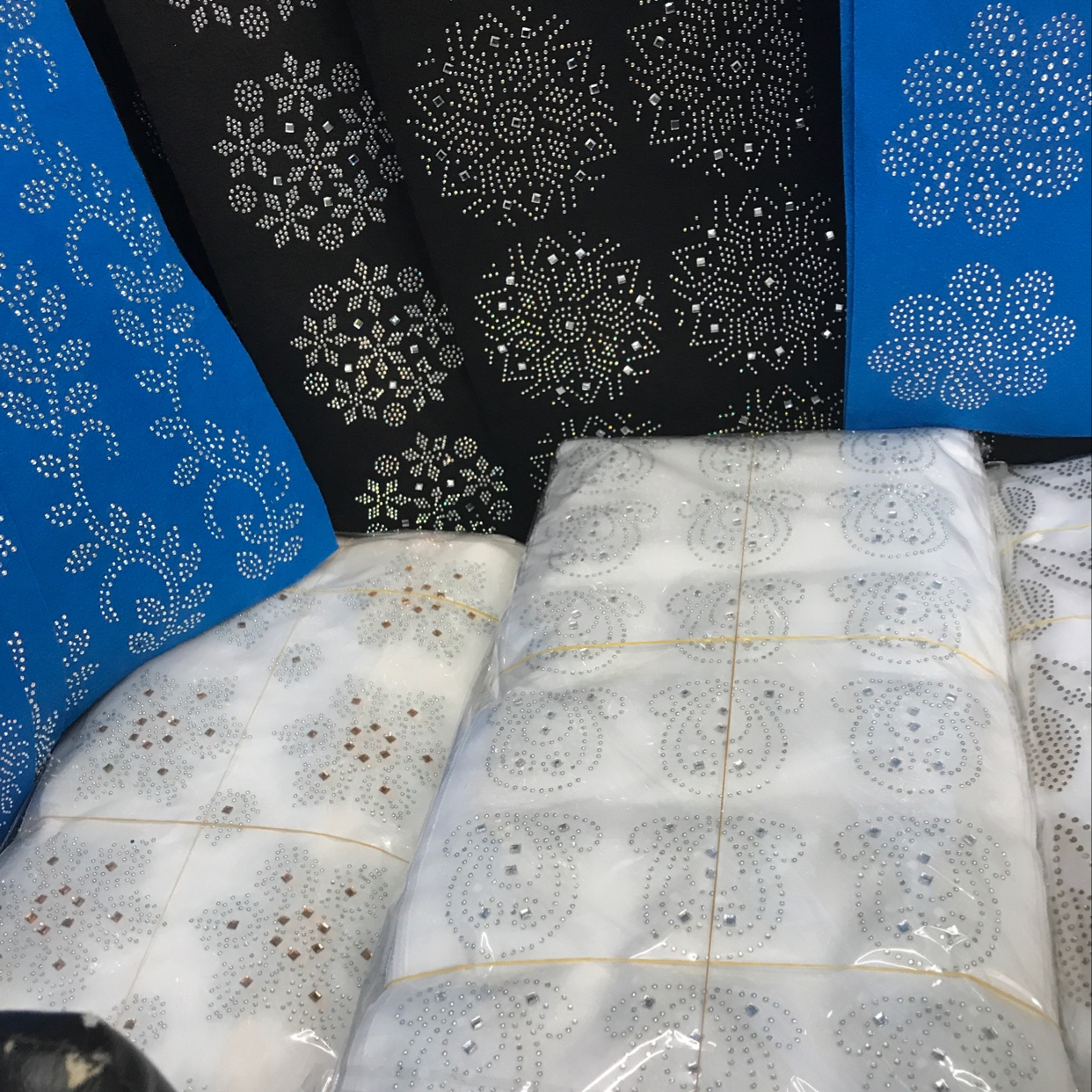
New Era of High Temperature Technology: Overview of Hot Drill and Hot Pull Technology
First of all, we will enter the world of hot drilling and hot drawing to understand the basic concepts and development process of these two technologies. As an emerging high-temperature process, they stand out with higher precision, faster speed and lower cost, and have gradually become a hot topic in the industry. Compared with traditional mechanical cutting or chemical etching, hot drilling uses high energy density beams to remove materials, while hot drawing is the operation of local heating and deformation of metals or other substances under controlled conditions. Both can complete delicate tasks without damaging the surrounding tissue, so they are widely used in a variety of applications that require precise control.
Scientific Disclosure: Exploration of the Principle of Hot Drilling and Hot Drawing
In-depth discussion of the specific working mechanism of hot drilling and hot drawing, we can find that there is a wealth of physics knowledge. For example, hot drilling mainly depends on the energy distribution characteristics of laser focus. When a strong pulse is irradiated on the target surface, it will produce an instantaneous extremely high temperature gradient leading to evaporation or melting. At the same time, hot drawing makes plastic flow of the treated part to form the required shape change by precisely controlling the heat input. These seemingly complex theories have actually been perfectly embodied in many practical cases-from micron-level integrated circuit wiring to large aero-engine blade molding.

Wide range of applications: from jewelry to high-tech manufacturing
Nowadays, hot drilling and hot drawing are no longer limited to a single field, but are active in many important industries and play a key role. In the jewelry making process, the former can be used for precision cutting of raw stones and polished into dazzling finished products; the latter can shape complex and exquisite bracelet links. In the electronics industry, it depends on these two to realize the wiring laying on the microchip packaging test platform or the fine routing pattern drawing on the flexible circuit board. Especially in the face of increasingly refined small parts production needs, only such high-level special processing methods can meet the quality requirements under strict standards.

Highlights of technological innovation: a new driving force for industrial upgrading
Looking back at the major scientific and technological innovation events related to hot drilling and hot drawing in the past few years, we can see that scientists have always maintained an attitude of unremitting pursuit of progress. On the one hand, a large number of new patents have emerged covering improved optical element designs to enhance output power stability; on the other hand, there are also many basic research results that have helped to make substantial progress in the development of new materials such as ultra-high temperature ceramic coatings. Looking ahead, under the guidance of artificial intelligence-assisted optimization algorithms, it is expected that more possibilities of subverting imagination will emerge, such as adaptive dynamic adjustment of focal length range to expand the coverage of applicable object types and so on. All of this will inject a steady stream of vitality into the entire industry chain, and attract more companies and talents to join them to create a brilliant tomorrow.

Practice tests true knowledge: user feedback witness quality
Ultimately, it's time to get back to reality and look at the value of any advanced technology. Many people in the industry have expressed their views on hot drilling and hot drawing: a senior craftsman praised that "this tool makes my work more delicate and vivid"; another engineer said that "it greatly shortens the product development cycle and improves market competitiveness". In fact, it is precisely because of the existence of many positive reviews that such a bright future has been forged today. Through the study and analysis of specific cases, it is not difficult to see that there are unparalleled advantages in improving work efficiency or reducing costs. In addition, many excellent customers are willing to share their stories about why they chose this new technology in the first place and how they benefited from it. Together, these voices have come together to form the strongest supporting body of evidence that hot drilling and hot drawing are indeed trustworthy options.
